The Hidden Costs of Unused Forklift Batteries—and How to Solve Them
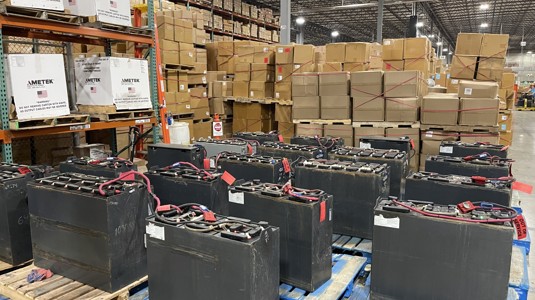
Forklift batteries are critical assets in warehouse operations, yet they frequently go unused due to factors such as overlooked maintenance, damaged battery or charger components, and inefficient management practices. These neglected batteries often accumulate in what's commonly referred to as a 'battery boneyard.' This scenario isn't merely a visual nuisance; it represents significant tied-up capital and continuous maintenance expenses. Moreover, batteries sitting idle without proper care degrade much faster, shortening their useful lifespan and leading to costly, premature replacements.
The financial impact of unused forklift batteries is frequently underestimated by businesses. While the immediate expenses related to battery replacements or repairs are tangible, companies often overlook the indirect, yet substantial productivity losses. Forklift operators forced into frequent battery changes spend less time on the primary job of moving products. This inefficiency creates unnecessary downtime, interrupting workflows and slowing overall warehouse productivity. One compelling example comes from a large distribution center, which reported a remarkable 20% reduction in battery changes and saved over $160,000 annually after addressing their battery management practices.
Understanding the problem fully requires recognizing that battery mismanagement is not just about asset count but also about usage patterns and maintenance routines. A detailed analysis involving over 10,000 batteries demonstrated an insightful revelation: battery age alone isn't a reliable indicator of performance or remaining lifespan. Instead, the primary factors impacting battery effectiveness and longevity are related to improper or neglected maintenance practices, such as inconsistent watering, overheating, and inadequate inspections.
Given these insights, fleet managers can significantly mitigate the hidden costs of unused forklift batteries by embracing several proactive, data-driven management strategies:
1. Identify Unused Batteries:
Effective battery management starts with accurate, regular monitoring of battery usage patterns. Managers need clear visibility into which batteries are sitting idle and why. Immediate, routine inspections can reveal straightforward issues—such as damaged cables, broken connectors, or unaddressed repairs—that, if promptly corrected, can bring the battery back into service quickly. Identifying idle batteries is the critical first step toward reducing battery-related expenses and improving fleet efficiency.
2. Use Data to Drive Decisions:
Traditional decision-making often depends heavily on anecdotal feedback from operators or outdated assumptions regarding battery lifespan based purely on age. Instead, fleet managers should adopt real-time, data-driven monitoring tools to accurately measure battery availability and run times. Real-time analytics help pinpoint underperforming or problematic batteries before they lead to downtime. This proactive approach significantly enhances operational efficiency and reduces unexpected interruptions.
3. Implement Proactive Maintenance:
Adopting a rigorous, data-supported preventive maintenance schedule can dramatically increase battery lifespan and reliability. Simple yet critical maintenance tasks—like proper watering, periodic inspections for corrosion, and monitoring charging habits—can extend battery life significantly. Software systems designed specifically for battery fleet management provide automated alerts, maintenance reminders, and performance analytics that ensure batteries are consistently maintained at optimal levels. Companies investing in these tools often realize substantial cost savings and efficiency gains.
4. Optimize Fleet Size:
Many companies rely on historical rules-of-thumb to determine their battery fleet size—such as maintaining two batteries per forklift—without regularly reassessing actual usage and needs. However, a more strategic, data-informed approach to fleet sizing can prevent significant overspending on unnecessary batteries and their associated infrastructure. By continuously evaluating actual usage data, companies can maintain an optimal number of batteries, avoiding the hidden costs and inefficiencies associated with excess or insufficient battery inventory.
Effective forklift battery management, although it may seem initially daunting, is entirely achievable and highly beneficial when driven by contemporary strategies and technological solutions. Leveraging modern tools and adopting proactive approaches to battery management can lead to significant reductions in hidden costs, improved productivity, and considerable long-term savings.
Ultimately, the essential message for fleet managers is one of strategic optimism. Companies committed to actively monitoring, maintaining, and intelligently managing their battery assets will quickly realize measurable improvements in both operational efficiency and their financial performance. By transitioning away from outdated management practices and embracing a data-driven, proactive approach, businesses can uncover substantial hidden value, turning what was once an overlooked challenge into a genuine competitive advantage and a significant area of cost reduction and increased productivity.