Improve your productivity and profits
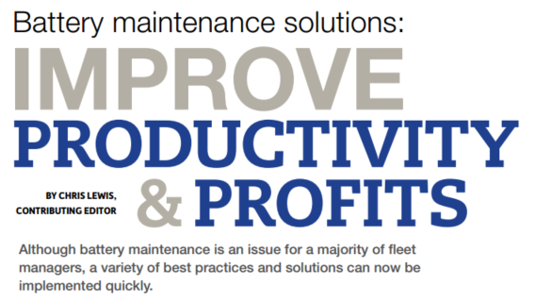
Battery maintenance has become a topic of increasing concern for fleet managers. After all, if batteries are poorly maintained, they will typically die quickly and result in a considerable loss of money.
But, there’s even more to the issue. If the batteries can’t hold a charge, forklifts can’t be used as long as they should be—forcing operators to either exchange their trucks or replace the batteries. This loss in time then leads to a loss in productivity that is ultimately far more expensive than the actual maintenance of the batteries.
“High costs also prevent the masses from receiving the most critical information they need for day-to-day operations, particularly information pertaining to programs that power trucks,” says Lynda Stephens, director of information solutions for EnerSys.
By implementing these best practices and solutions, fleet managers will increase profit margins and decrease downtime, but will improve battery run times, reduce battery changes and enhance battery life.
Cost-effective, timely battery maintenance
To optimize battery maintenance capabilities, fleet managers should first assess the site and the application in which their battery chargers will be used, so they can decide which chargers provide the best value, given the conditions. It is also important to monitor aspects such as the battery’s charge curve, equalization schedule and electrolyte temperature, as well as its efficiency and performance while performing preventative maintenance on a regular basis throughout batteries’ lifetimes.
A range of battery management solutions can be applied in days or even hours. For instance, if fleet managers are swapping their batteries, they may use a first in, first out (FIFO) system so they can manage their batteries as they are charged, cooled and watered prior to being used. In doing so, operators will use the batteries that are the most appropriate for maximizing lift truck productivity and extending run times.
Fleets with multi-shift usage may also use “smart” chargers, especially fast and opportunity chargers, rather than conventional charging solutions that don’t have closed feedback loops or other features necessary to ensure that batteries are well maintained and protected. According to Jonah Teeter-Balin, director of product marketing and efficient energy systems for AeroVironment, the chargers should also be multi-voltage, so that any truck with any battery can be charged, monitored and properly maintained.
Whatever the charging system, all batteries should also be equalized and watered once a week. Batteries must not be over-discharged, as that will shorten battery life. Over-discharging occurs below 20% to 30% of battery capacity for lead acid batteries.
“Ensuring a proper charge heavily relies on the warehouse’s lift truck operators, as they play a vital role in maintaining the battery and charger health because they are often the first to identify a problem as soon as it occurs,” says Jim Lichtenberg, business manager for Ametek Prestolite Power. “By inspecting the battery and charger equipment each day, the forklift operators can help identify a problem before it develops into a more serious issue. Such awareness by forklift operators improves safety, helps limit downtime and increases a warehouse’s overall efficiency.”
Fleet managers may also choose to outsource tasks, such as watering and testing batteries, to power management companies and battery providers. In addition to performing these tasks, some outsourcers also provide 24/7, remote battery monitoring. This monitoring allows them to organize and analyze crucial data and provide advice about improving batteries’ performance and longevity.
According to EnerSys’ Stephens, these types of programs have the ability to manage every aspect of a battery’s operation, so the battery program is handled in totality.
“Infrequently used vehicles that keep the battery in the truck to charge often are orphaned from proper equalization, watering and even discharging and charging,” Stephens says. “They end up parked off in a corner and missed during weekly battery management. This means the batteries can end life early, even though utilization is extremely low. Good record keeping can prevent this issue.”
According to Stephens, one- and two-shift operations are less vulnerable to issues like improper charging, missed equalization and watering, as there is typically enough time every day to address such battery management needs. Consequently, managers will usually be able to achieve long, full battery lives.
But three-shift operations are much more susceptible to these issues, as proper battery management may be sacrificed for a higher level of productivity. Outsourcing may be a good response to these issues, though, as it can help reduce the risk of early battery failure from inadequate battery management and high maintenance costs.
BDRs, clouds and watering
As fleet managers continue to seek new solutions to improve battery maintenance, battery specialists are now offering an array of technologies. Battery data recorders (BDRs), in particular, are becoming popular. According to Ryan Lynch, vice president of corporate services for ABT Power Management, BDRs can offer fleet managers various types of information depending on their sophistication and sensors. Each BDR is placed directly on a battery. Some are able to measure amperage, electrolytes, temperature and water level, while others are used to connect to sophisticated chargers, thereby improving the flexibility of battery charging.
Some battery specialists also provide Internet of Things smart solutions that allow them to work with any type of BDR, so they can provide equipment and power solutions that are best suited for each customer’s unique environment and application needs.
“Data is the lifeblood of our solutions and drives the impact we have on our customers’ operations. Our Internet of Things solution has charger and battery data spanning over a dozen years and 50 million records,” Lynch says. “Without leveraging this data in an action-oriented way, we would not be able to reduce most facilities’ power assets by up to 30% and extend the life of the remaining power assets by up to 30%.”
Cloud-based solutions are also available, ranging from 24/7 battery operations management programs that collect data and analyze operations metrics to full monitoring devices that feature dashboards visible to battery users and providers. Such dashboards allow fleet managers to monitor their batteries from desktops, laptops, smart phones and tablets, and determine the information they prefer to see and alerts they desire to receive, resulting in a more personalized product for each customer, says Dean Portney, vice president of sales and marketing for Hawker.
Watering is another crucial component of battery maintenance, as various aspects are involved to ensure the process is conducted correctly. First, the water should be pure and deionized with low suspended solids. Watering should also be completed at the correct time, according to Harold Vanasse, vice president of sales and marketing for Philadelphia Scientific. Battery watering monitors specify exactly when batteries should be watered, which prevents under- or over-watering and ultimately increases the batteries’ longevity, Vanasse says.
“Watering batteries by hand is a laborious, time-consuming process. Single-point watering systems water batteries in precisely 15 seconds—a fraction of the time involved with hand watering, and eight times faster than filling a battery with a float-based watering system,” Vanasse says. “Single-point systems improve safety and environmental cleanliness, too, by eliminating the possibility of accidental overfilling, resulting in battery acid spills.”
The single-point water systems feature valves on top of each cell, which can then turn off whenever the correct watering level is achieved. As a result, employees’ exposure to sulfuric acid is not only significantly reduced, but watering is also completed more accurately and efficiently.
Battery room management systems
Some warehouses and DCs also use battery room management systems. The systems offer fleet managers data about the number of batteries they currently have as well as the total number they need. Consequently, the managers have improved workplace productivity, while reducing operational costs.
“We have seen battery rooms reduce their battery fleet by 30% when they use the data from the systems that proves they are not running out of batteries,” Vanasse says. “It’s no longer guesswork, which usually errs on the side of having too many batteries.”
Vanasse advises fleet managers to install the battery room management systems before they make further purchasing decisions. Oftentimes, fleet managers will purchase new batteries based on the age of their battery fleet. When this occurs, they may purchase too many batteries for their pallet jacks and not enough for turret trucks or vice versa. The systems can eliminate this issue once and for all.
“When fleet managers use battery room management systems to properly rotate their batteries, they will have more time available for cool down, while also delivering more power to their trucks,” Vanasse adds. “Typically, warehouses and distribution centers that install the systems will also notice faster battery changes (usually two to five minutes faster), fewer battery changes (10% to 20% less), a longer battery run time (30 minutes) and a longer battery life—often over six months more.”
The future is now
New technology is being developed to use the specific gravity of a battery’s electrolyte to track the most accurate state of charge and ensure the battery is not overused. Among other aspects, the technology will measure cell balance, electrolyte level and temperature, and volts per cell.
“A proposed new measure takes into account the electrolyte’s specific gravity—the ratio of the weight of the battery electrolyte, as compared to an equal volume of water,” Ametek Prestolite Power’s Lichtenberg says. “It is the most accurate measure of state of charge.”
By using each of these measurements, the technology is expected to prevent unnecessary battery charging, reduce the costs of battery replacements, improve the efficiency of manufacturing and warehousing operations, and actively manage batteries throughout their lifetimes.
Opportunity charging or fast charging may not be ideal in every facility; in fact, most facilities have many different scenarios that require a variety of conventional and fast-charging applications. To determine which charging application is appropriate and will offer the lowest total cost of ownership, some battery specialists are not only using data analysis to choose the most effective application for each respective situation—they are also developing hybrid solutions.
“One charger, in particular, will conventional, opportunity and fast charge with patented charge profiles, as it is powered through a modular design,” says Hawker’s Portney. “This modular design, in turn, offers scalability, flexibility and power redundancy.”
Read the article here on the https://www.materialhandling247.com/ website