How much a battery costs per hour? Making the right financial decisions in uncertain times.
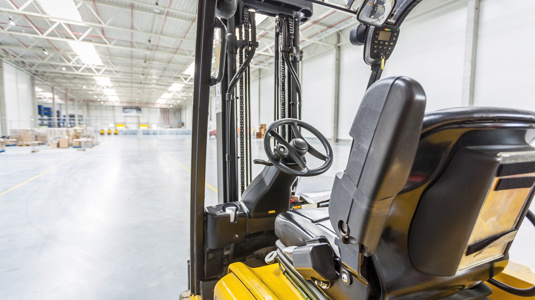
MONTGOMMERYVILLE, PA, November 16th 2020: It’s been a hard year to predict. The figures that are going to be used to forecast 2021 and the years that follow are going to take some time to navigate! But the world keeps on turning, and that means everyone will have to take a slightly more realistic approach when creating a roadmap for the future.
Planning and coordinating the energy requirements needed to keep an operation running smoothly is no exception. The increase in logistical demand from e-commerce sales doesn’t look like it’s going to slow down over the years to come, the pandemic has brought the way people shop into sharp relief.
With a plethora of choices available on how to store energy, one of the most important factors to consider in uncertainty, is cost. With the sales line having peaks and valleys over the past few months, having a clear understanding of the true cost of purchasing, charging and using batteries is one clear path we can take to make the right decision.
So, we have decided to look at how much a battery costs per hour. We’ve used the data generated by the products Philadelphia Scientific manufactures to maximize the performance of lead-acid batteries, alongside the facts and figures given from lithium ion suppliers in our calculations.
The new generation of lithium batteries are being offered now with a guarantee of 10,000 working hours. We’ve taken that as a base point and calculated this in comparison to an equivalent lead-acid battery.
So, if a lead-acid battery for an order picker costs $4000 and with a 10,000-hour guarantee, that works out to a cost of $0.40/hour for storing that energy. If you add in the maintenance costs to keep them running as they should be, the total cost would average to $0.60/hour.
If the equivalent lithium battery costs $11,000 with the same 10,000-hour guarantee that equates to a cost of $1.10/hour cost. That gives you two options and two clear cost points:
- Fully maintained flooded lead acid - $0.60/hour
- Maintenance free lithum - $1.10/hour
Now that’s on a single battery. The increase on logistical demands has meant that more trucks and batteries are needed to keep everything running smoothly.
Taking a 20 lift truck site that runs an average of 2000 hours per year:
- Fully maintained lead acid - $104,000.
- Lithum-Ion - $220,000.
So, over a 5-year period running at 10,000 hours, the costs work out to be:
- Fully maintained lead acid - $20,800/year.
- Lithum-Ion - $44,000/year.
That’s a total cost difference of $116,000 just on purchase and running the batteries, it doesn’t include any of the additional charger & infrastructure costs needed. This data isn’t a secret. It’s available to anybody and everybody. We understand that different battery technologies are suited to different applications and there isn’t a one size fits all, especially in uncertain times
As you can see there is a considerable difference in costs between Lithium-Ion and lead-acid batteries but that’s not the only factor to consider. Both options have their pros and cons. While Lithium-Ion maybe maintenance free it does involve following a strict charging regimen, lead-acid batteries need maintaining, equalization and handling on larger operations.
For the single forklift truck at the back of a store, Lithium-Ion would likely be perfect. Plug it in at the end of the day and it's ready to go at the start of the next. Simple. If the operation is a lot larger, running two or even three shifts, then it gets a little more complicated. Due to the way that Lithium-Ion batteries store and release energy, to get the best performance out of them, they need a consistent charging regimen to be followed. The trucks will need to plugged-in on breaks and lunches to maintain their charge, making sure that the voltage doesn’t drop and leave the truck stuck in an aisle. In larger operations, this means that there needs to be both space and the infrastructure available to charge the batteries regularly, the training to follow the charging regimen and the ability to meet the costs of the increased energy demand. There are a lot of separate components that need to be considered with a full Lithium-Ion operation, but it does eliminate the need for maintenance and handling.
A lead-acid battery in a single forklift truck at the back of the store, in all likelihood, isn’t going to last anywhere near as long as it should because maintenance is probably going to be pretty low down on the priority list. This can lead to the battery drying out, sulphating and in turn, not lasting anywhere near as long as it should. On larger operations, while lead-acid acid batteries need maintenance, there are tools and processes available to reduce maintenance time, leading to a total cost of less than $25 cost over the lifetime of a battery. It does require an area for battery changing, but in most cases, this is smaller than the space needed to charge a shift's worth of Lithium-Ion trucks. A truck using a lead-acid battery can also go from empty to full in under 4 minutes with a battery change, and the empty battery can be charged at more optimal times in the day so power is not being drawn at peak times. There are also products available that can split the chargers, effectively doubling the charger capacity without the need for additional infrastructure. Not only will this save a considerable amount of capital, but it also allows an operation to expand capacity quickly and easily.
As you can see there are pros and cons to both, ultimately this decision comes down to what is best for any given operation. So, if price is your beacon, then hopefully this data can help shine a light and help you make the right financial decisions.
If you’d like more information on what data our products can offer you visit https://www.phlsci.com